There are a huge range of stick welding electrodes to choose from, but the most commonly used for mild steel are E6010, E6011, E6013, E7018 and E7024. All of these have different properties and are best suited for different applications.
For example, some electrodes need to be used on clean metal, some have deep penetration, some can only weld in certain positions.
This guide compared these most popular welding electrodes to help you choose the right one for your application.
Contents
Welding Rod Comparison Tables
Welding Rod | Current | Positions | Penetration | Slag | Use on rust | Summary |
---|---|---|---|---|---|---|
6010* | DC+ | All | Deep | Thin | Yes | Good for tacking. Pipe welders electrode. |
6011* | DC+ AC | All | Deep | Thin | Yes | Similar to 6010 but with AC. Good for repairs. |
6013* | DC+ DC- AC | All | Shallow | Heavy | No | Easy to run. For beginners on clean sheet metal. |
7018* | DC+ AC | All | Medium | Heavy | No | Used in structural welds. |
7024* | DC+ DC- AC | Flat, Horizontal | Medium | Heavy | No | High deposition for high-speed flat fillets. |
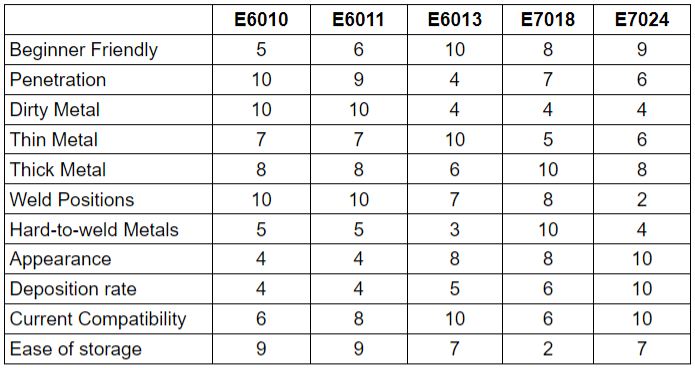
6010 welding rods
E6010 welding rods are electrodes that are known for being the most penetrating arc you can get and their ability to dig through rust, dirt and paint.
Striking 6010s is really easy, which makes them a great option for tack welding. They also only leave a thin layer of slag which is easy to chip off.
6010 electrodes run a tight arc and have a thinner penetrating bead, which can make them difficult for beginner welders to handle. However, they are popular with experienced welders and fabricators, and are primarily used by pipe welders for welding root passes and fill passes.
6010s are important for pipe welders because of their deep penetration, but this level of penetration isn’t needed for most hobbyists and general fabricators.
Their ability to cut through rusted and dirty metal also makes them a decent choice for repair work because you don’t have to clean up the metal before using them. However, many welders will opt for 6011s instead
Finally, 6010s can only be used on DCEP power, so you won’t be able to use these with an AC stick welder.
Pros of 6010 electrodes
- Good for tacking
- Suitable for welding rusted or painted metal
- Good for filling gaps
- Deep penetration
- Can be used in all positions
- Thin slag that’s easy to remove
- Quick-starting arc
- Common in fabrication, repair and pipe welding.
Cons of 6010 electrodes
- Difficult to run for beginners
- Not suitable for AC
- Some inverters won’t run them
Below is an explanation of what the digits in E6010 welding rods mean.
Letter/Number | Meaning |
E | Electrode |
60 | Tensile strength is 60,000 pounds per square inch. |
1 | Welds only all positions. Flat, horizontal, vertical and overhead. |
10 | Welds DC+. High cellulose sodium coating. |
6011 welding rods
E6011 electrodes are the close sibling of 6010s but have a different coating which allows them to be used on AC as well as DCEP, unlike 6010s which can only be used on DCEP.
This versatility makes them a great rod to have around because they can be used with any stick welder as well as being used in any position and for welding on rust, paint or oily metal.
6011s are really close in characteristics to 6010 and produce deep penetration, however, they provide slightly less penetration than 6010s and the arc is a bit easier to keep stable. This is why 6010s are more popular with pipe welders, but general fabricators often use the more versatile 6011s.
Overall they’re a good option for a general-purpose rod that gives strong welds without much slag.
Pros of 6011 electrodes
- Good for tacking
- Suitable for welding rusted or dirty metal
- Good for filling gaps
- Deep penetration
- Can be used in all positions
- Thin slag that’s easy to remove
- Quick-starting arc
- Common in repair and general fabrication
- Can run DC and AC
Cons of 6011 electrodes
- Difficult to run for beginners
- Some inverters won’t run them
Below is an explanation of what the digits in E6011 welding rods mean.
Letter/Number | Meaning |
E | Electrode |
60 | Tensile strength is 60,000 pounds per square inch. |
1 | Welds only all positions. Flat, horizontal, vertical and overhead. |
11 | Welds AC, DC+. High cellulose potassium coating. |
6013 welding rods
E6013 is the rod that most people use when starting out because stabilizers in the coating make them very forgiving. They give a smooth bead and provide good quality welds with minimal spatter and can be used in any position on AC or DCEP.
6013s offer shallow to moderate penetration. They don’t penetrate as well as 6010, 6011 or 7018 but deposit metal quickly and easily. This makes them a good choice for multi pass welds where layers can be built up and deep penetration isn’t required.
They do not dig through rust or dirt like the 6010 and 6011, so you will need to either clean up the metal or use these or new metal. These are usually used on new, clean sheet metal. 6013s also leave a heavy slag covering but the slag is really easy to remove.
Overall they’re an easy rod to use that’s good for welding on thin material, clean sheet metal and multi pass welds.
Pros of 6013 electrodes
- Can be used in all positions
- Suitable for AC and DC
- Arc is easy to maintain
- Good for welding at lower amperages
- Produces a clean weld bead
- Low spatter
- Slag is quick-freezing and easily removable
- Common in general-purpose welding and light fabrication.
Cons of 6013 electrodes
- Produces a lot of slag
- Not suitable for rusty or dirty metal
- Low penetration
Below is an explanation of what the digits in E6013 welding rods mean.
Letter/Number | Meaning |
E | Electrode |
60 | Tensile strength is 60,000 pounds per square inch. |
1 | Welds only all positions. Flat, horizontal, vertical and overhead. |
13 | Welds AC, DC+. High titania potassium coating. |
7018 welding rods
E7018 electrodes have a thick flux with low-hydrogen content, making them easy to use with a smooth arc. They produce high-quality welds with minimal spatter, medium penetration and large, strong, less defined weld beads.
The medium penetration means when cannot be used on rusty or dirty metal. They are most commonly used in structural steel welding. Any tall buildings you see around you will probably have been built with 7018 electrodes. 7018 produces strong welds on harder to weld steels including carbon steel and high-strength steel base metals in low or high temperature environments.
They are versatile electrodes that can be used in all positions on AC and DC (usually DC). Heavy slag covers the weld when using 7018s, but this slag will peel off in massive chunks so it’s not a problem.
The main problem with 7018 electrodes is that they need to be stored at 250 degrees F once they have been opened and in a low-humidity environment where no moisture can get into the electrode. The best place to store them would be in an electrode rod oven. Once you’ve opened the box they’ll only be usable for a few hours unless they go in an oven.
Pros of 7018 electrodes
- Can be used in all positions
- Suitable for AC and DC
- Smooth arc that’s easy to maintain
- Minimal spatter
- Medium arc penetration
- Commonly used in structural welding
Cons of 7018 electrodes
- Not suitable for rusty or dirty metal
- Heavy slag
- Need to be stored away from moisture
- Need to be stored at 250 degrees F once opened
Below is an explanation of what the digits in E7018 welding rods mean.
Letter/Number | Meaning |
E | Electrode |
70 | Tensile strength is 70,000 pounds per square inch. |
1 | Welds only all positions. Flat, horizontal, vertical and overhead. |
18 | Welds AC, DC+ and DC-. Low hydrogen potassium, iron powder coating. |
7024 welding rods
7024 welding rods are perfect for laying down fast fillet welds in the horizontal and flat positions on AC or DC.
They have a thick flux coating which results in high deposition rates with a big weld puddle. The arc is stable and easy to use and the penetration is medium with minimal spatter and porosity. The result is a slightly convex rippled weld bead that’s perfect for single pass fillet welds. It works a treat on thick metal and is regularly used on heavy construction equipment.
A lot of heavy slag is created when using 7024s, but this slag mostly self-cleans. This is why you can’t weld overhead because it will start raining down hot slag on you. You also need to weld on clean metal because it won’t dig through rust or dirt.
Overall they’re perfect for high-speed flat and horizontal fillet welds, especially on clean steel plate over ¼ inch thick.
Pros of 7024 electrodes
- Nice looking weld bead appearance
- Can run on AC and DC
- Medium penetration
- Fast welding with high deposition rates
- Partly self-releasing slag
- Good for fillet welds
- Good striking ability
- Stable arc
- Low spatter
Cons of 7024 electrodes
- Not suitable for welding overhead or vertical
- Creates a lot of slag
- Not suitable for rusty or dirty metal
Below is an explanation of what the digits in E7024 welding rods mean.
Letter/Number | Meaning |
E | Electrode |
70 | Tensile strength is 70,000 pounds per square inch. |
2 | Welds only in flat and horizontal |
24 | Welds AC, DC+ and DC-. Rutile, iron powder coating. |