When stick welding, you’ll need to know what the different types of stick welding electrode numbers mean and what applications they’re suitable for. Some of the key considerations are welding materials, welding position, polarity and penetration.
Below is a chart of the different types of stick welding rod and explanations of what the different numbers mean. We have gone into this in more detail below.
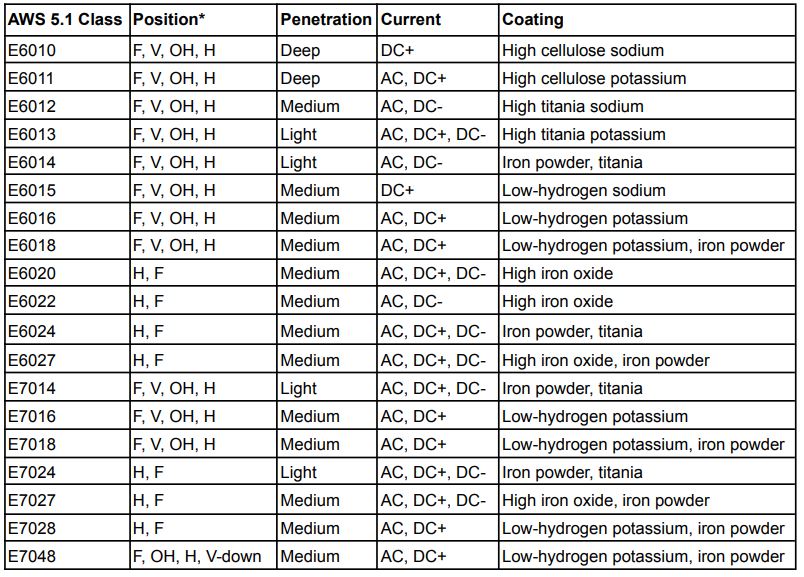
Click here to see the welding rod chart in PDF format.
Contents
Common Stick Welding Rods
You’ll tend to find there will be certain welding rods that you regularly see in the shops and find yourself using time and time again. The most common types of welding electrodes for mild steel are E6010, E6011, E6013, E7018 and E7024.
- E6010: Pipe welders electrode. Deep penetration, good on rusty metal. DC+ only
- E6011: Similar to 6010 but with AC capabilities. Good for repairs.
- E6013: Versatile and easy to run. Low penetration.
- E7018: Strong welds on clean metal. Commonly used in structural welding.
- E7024: High deposition, only suitable for flat and horizontal welds.
Further reading: Comparison of 6010, 6011, 6013, 7018 and 7024 electrodes.
AWS Classification Numbers Explained
The American Welding Society (AWS) has created a numbering classification 5.1 that is the most commonly used way of differentiating between stick electrodes. The numbers in the classification refer to the properties of the electrode and how it can be used for the best performance.
The welding rod classification numbers for mild steel stick electrodes are set up in the following way.
The Prefix “E”
“E” stands for welding electrode. It simply denotes that it is a stick welding electrode. It might seem like it’s stating the obvious, but not all welding rods used as electrodes, such as TIG welding rods.
The first two digits
The first two digits of a 4-digit welding rod number indicates the minimum tensile strength of the electrode in thousand psi. In other words, one square inch of weld metal would not fail until over 60,000lbs force is applied. For example:
- E6010: Has minimum tensile strength of 60,000 psi
- E7018: Has minimum tensile strength of 70,000 psi.
In a rarely seen 5-digit number, it will be the first three digits of the welding rod number. For example:
- E10018: Has a minimum tensile strength of 100,000 psi.
Next to Last Digit (usually 3rd)
The next digit (usually 3rd digit) indicates the positions that you can use the electrode.
“1” means that it can be used in all positions, “2” means it can be used in flat and horizontal positions only, “3” in flat position only, and “4” means it can be used in flat, horizontal, vertical down and overhead. For example:
- E6013: Can be used in all positions
- E7024: Can be used in flat and horizontal positions only
- E6030: Can be used in flat position only
- E7048: Can be used in flat, horizontal, vertical down and overhead.
The final two digits
The final two digits combined. The last two digits together indicate the correct current to use and the type of flux coating. The current refers to whether it can be used on an AC or DC stick welder.
Below is an example of how the full welding rod numbers look when put together for an E6010 electrode.
Letter/Number | Meaning |
E | Electrode |
60 | Tensile strength is 60,000 pounds per square inch. |
1 | Welds only all positions. Flat, horizontal, vertical and overhead. |
10 | Welds DC+. High cellulose sodium coating. |
Welding electrode flux coatings explained
Different numbered welding rods contain different flux coating as outlined in the chart above. These elements impact the welding operation in different ways.
There are lots of different elements in the flux coating, but these are usually divided into three categories: Cellulosic, titania/rutile, and low-hydrogen.
Cellulosic welding rods
Cellulosic rods are any welding rods which contain a high amount of cellulose, such as cellulose sodium E6010 and cellulose potassium E6011. The following are key characteristics of cellulosic rods:
- Cellulosic rods contain a lot of hydrogen which creates a powerful digging penetration.
- There are low amounts of slag
- They are fast freezing electrodes and good for welding in all positions
- Good for welding on rusty, oily or painted metal.
- Arc is hard to control and not suitable for beginners
- More spatter and fumes
- Some inverter welders can struggle with them
Titania/rutile welding rods
Titania/rutile rods are any welding rods which contain a high amount of titania, such as E6013, E7014 and E7024. The following are key characteristics of rutile rods:
- Stable arc that’s easy to weld with
- There is only light penetration
- Good for welding thinner metals
- Low spatter and fumes
- Cannot weld rusty or dirty metal
- Not suitable for structural/high performance welds
Low-hydrogen welding rods
Low-hydrogen rods don’t contain any cellulose or rutile materials or materials that contain a lot of hydrogen. The following are key characteristics of low-hydrogen rods:
- Great bead appearance
- Slag is very easy to remove
- High ductility with low levels of impurities
- Best for harder to weld steels
- Not suitable for dirty metal
- Fumes can be harmful
- Welding rods need special storage
Summary of electrode coatings
- Cellulose sodium (Exx10). Cellulose burns and generates a shielding gas to prevent oxidation and produces a digging arc with deep penetration.
- Cellulose potassium (Exx11). Similar cellulosic material to cellulose sodium but uses potassium instead of sodium which causes ionization of the arc and allows for AC welding.
- High titania sodium (Exx12). Titanium helps give a smooth weld appearance but with less penetration and less strong welds than cellulose based electrodes.
- High titania potassium (Exx13). Similar material to high titania sodium but uses potassium instead of sodium which allows it to be used on DC+
- Iron powder titania (Exxx4). Exx14 has 25-40% iron content. Deposition rate increases with iron content. Over 40% iron is not suitable for welding in all positions because of the deposition rate. Exx24 will have 50% iron content and have too high deposition to weld overhead.
- Low hydrogen sodium (Exxx5). Low hydrogen electrode that includes metal carbonates with no cellulose to give the best weld properties.
- Low hydrogen potassium (Exxx6). Similar material to low hydrogen sodium but with potassium instead of sodium which allows it to be used on AC as well as DC.
- Iron powder low hydrogen (Exxx8). This has the same coating as low hydrogen potassium but has increased iron content for better deposition which affect the position it can be used. Exx18 electrodes will have 25-40% iron power, Exx28 will have 50% iron powder because of the increase deposition rate.
- High iron oxide (Exx20). Iron oxide creates more slag with high deposition and a difficult to control arc.
- Iron power iron oxide (Exx27). 50% iron powder gives high deposition rates