Electrodes are one of the most commonly used items in welding. They are essential in stick welding, which is one of the easiest and most popular types of welding due to the portability of a stick welder and its ability to be performed without shielding gas.
Welding electrodes are basically a piece of straight, solid metal wire that is coated with a flux mixture. The electrode transmits an electric current which creates heat which melts the flux and protects the weld from contamination.
The article explains how these electrodes are created. Please take a look at this video which offers a great visual representation.
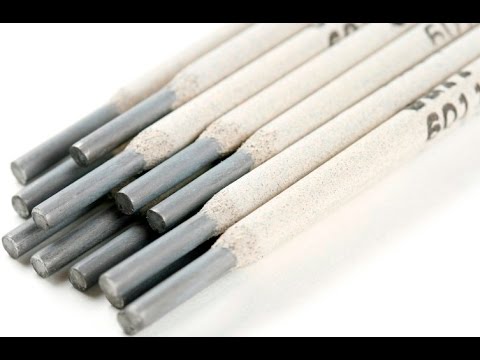
Contents
Forming the wire
The wire starts as an uneven roll of metal wire.The type of wire is usually stainless steel, but it depends on the electrode that is being made. The wire may be heat treated to increase its ductility. A metal forming machine will then pull the wire through drawing dies and shape the wire until it is uniform and completely straight at a set diameter.
Cutting the wire
The straight metal wire is then guided by metal rollers into a cutting device that chops the wire into equal segments. The length of these segments will vary depending on the type of electrode being produced, but will usually be approximately 12 inches. These equal pieces of wire will soon become the core of the electrode.
Making the coating
A dry mixture of elements must then be created to coat the metal wire and act as a flux. The mixture can contain nickel, manganese, iron, aluminum, titanium dioxide, mica, and limestone. A coloring agent will be added to help differentiate between different types of electrode. Potassium Silicate is then added to the mixture to wet the mixture and act as a bonding agent.
Adding the coating
The wet mixture is loaded manually into a hydraulic extrusion press. This will apply 120 tonnes of pressure to form briquettes. The wires are then fed into the extrusion press by rollers and coated by the flux mixture. The wires go through one at a time but at an extremely fast rate of up to 1000/minute.
Sanding the electrodes
The wire emerges fully coated, but it needs sanding before it can be used. The bottom couple of inches of flux is sanded away to create a piece of bare wire that can be gripped and the tip is bevelled to help better create an arc.
Inspecting the electrodes
Workers will manually check electrodes to ensure the coating is consistent and they appear as they should. Electrodes that fail manual review will be stripped of their flux and the wire will go back into the machine to try again.
Heating the electrodes
Once the electrodes have been quality checked, they are loaded into an oven to reduce moisture. The aim is to reduce moisture content to maximum 4% and can take up to 5 hours at over 900 degrees fahrenheit.
Grading the electrodes
Once the electrodes have cooled, they are fed through a printing press where the welding rod number and model are printed in addition to a colored strip to identify the type of electrode it is.
Packaging
Once all this is done they can be packaged and sent for shipping!
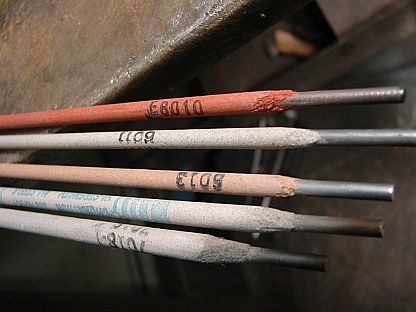